Can You Weld Aluminum with Laser?
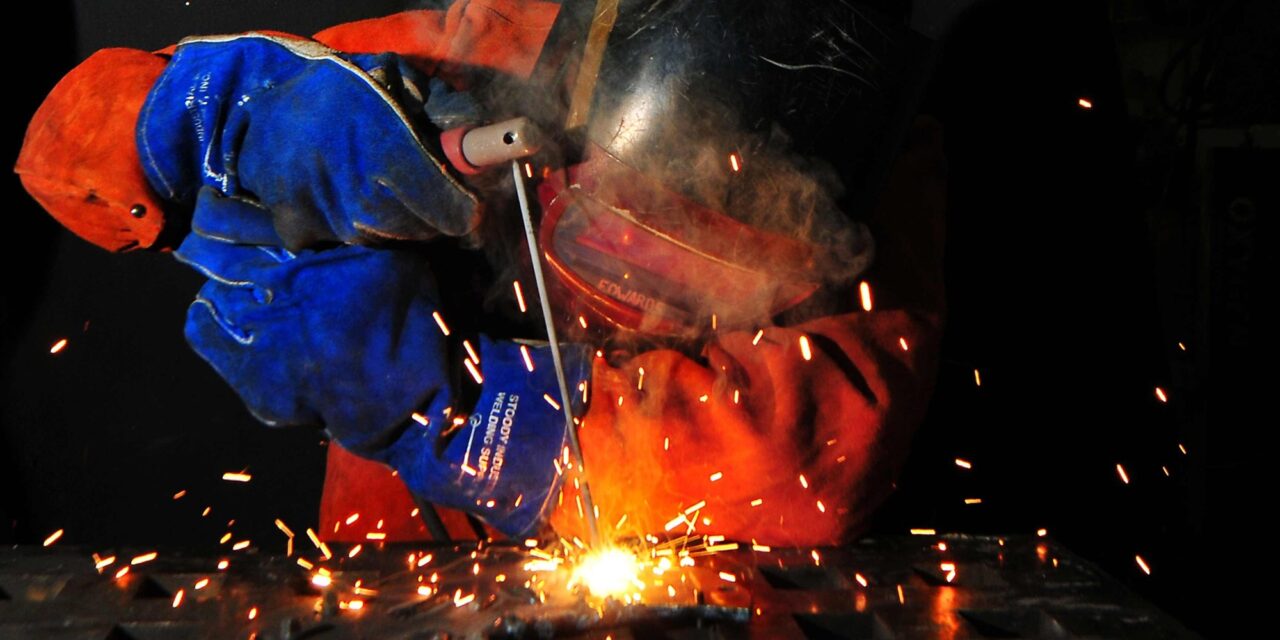
This article will describe the possibility of welding aluminum using this technique, the different types of lasers useful for welding aluminum, the benefits and constraints of laser welding aluminum, and some uses of laser welding aluminum in various industries.
Types of Lasers Used for Aluminum Welding
Laser Welding of aluminium alloys is a crucial process in the manufacturing of automotive vehicles, wireless communication equipment and countless applications involving lightweight and high strength structure materials.
Various classifications of lasers used for al-welding are possible, and they are all characterized by their advantages and disadvantages.
Some of the most commonly used lasers for this purpose include:
1. Fiber Lasers: This type of laser has recently found its way into aluminium welding applications as a result of its high efficiency and low costs of operation. The source has a high beam quality and can deliver high power in a localized area, which is important for welding thin aluminium foils. Also, as pointed out earlier, fibre lasers have high duty cycles, and the beam quality is very good for long distances; hence it is suitable for automation.
2. CO2 Lasers: CO2 lasers have long been used in welding aluminium. They have low cost and can produce high power levels, which can be useful when welding thicker aluminium sections. But, as output beam quality, they are not as good as fibre lasers, are more susceptible to degradation, need more maintenance, and have a lower duty cycle.
3. Solid-State Lasers: These lasers have lower power than fibre lasers but have greater beam quality. They are intended for welding thin aluminium sheets and where increased accuracy is needed.
Pros of Laser Welding Aluminum
Laser welding reveals the following advantages over other types of welding regarding aluminium.
Some of these advantages include:
1. High Precision: Automatic welding is less sensitive to weld pool movements and produces narrow welds with low distortion levels. This is especially important where thin aluminium foils are used because any heat introduced to the foils will lead to warping or the formation of other undesirable features.
2. Minimal Heat Input: Traditional welding procedures differ from laser welding since the latter has a small heat influence on the surrounding material. This minimizes thermal injury and makes it possible to join delicate components without causing heat-related failure.
3. High Speed: High speed of laser welding, reduces the labour cost. Furthermore, the laser beam contains high energy density, which ensures deep penetration welding suitable for welding thick aluminum sections.
4. Automation: Laser welding can be easily incorporated into an automated system; this could help increase productivity, reducing errors ands.
Laser welding Aluminum: Key Issues
However, as earlier mentioned, there are some drawbacks of laser welding aluminum, although the fact that this process has many benefits justifies its use.
Some of these challenges include:
1. Reflectivity: Aluminium has the issue of laser reflectivity since the material itself has reflective properties. This can cause a loss of energy, weld penetration, and efficiency decrease, as well as weld defects, such as keyholing or lack of fusion. The problem is solved in some laser welding systems by employing pulsed welding, which encompasses the modulation of the laser power density to enhance energy penetration.
2. Surface Oxides: Aluminum is easily oxidized to form a coherent oxide layer on the surface, which is nearly impossible to remove using the laser beam. To improve this latency, the aluminum surface must be prepared so that the surface is free of contaminants, which will interfere with the welding process and shield the weld area from surrounding atmosphere during welding.
3. Residual Stress: Cracking or warping can be caused by residual stress left in the welded material by laser welding. To reduce this problem, the welding process is to be tightly regulated; and in some instances, the post-welding heat treatment is likely going to be necessary.
Laser Welding and its Uses in Aluminum Industry and its Detail applications
Laser welding in aluminum involves the following: Some common applications include:
1. Aerospace Industry: Laser welding is used to join different parts including fuselage sections, wing panels and landing gear since aerospace most of its components from aluminum. Laser’s welding provides the accuracy and the required strength for such applications and at the same time reducing the weight of the component.
2. Automotive Industry: It is used widely in auto mobile industry currently since it is light in weight but stronger than steel. Most automotive companies today employ laser welding to connect aluminum parts including the skin, space frames, chassis and suspension systems, the benefits being it is very rigid, light and does not rust.
3. Solar Panel Manufacturing: Because aluminium is superb at transmitting heat and electricity, it is favoured in the production of solar panels. Laser welding is employed for the joining of the aluminum frame to the solar cells which produce a robust and assiduous yet lightweight construction that can endure the vagaries of outdoor settings.
4. Medical Devices: Owing to its biochemical compatibility and its ability to resist corrosion aluminum is commonly used in development of medical devices. Laser welding is employed to weld aluminum parts in the medical products including surgical tools, implants, and dentures to have a severe, flawless, and germ-free bond.