What are the 6 Most Common Metal Fabrication Techniques and Tools?
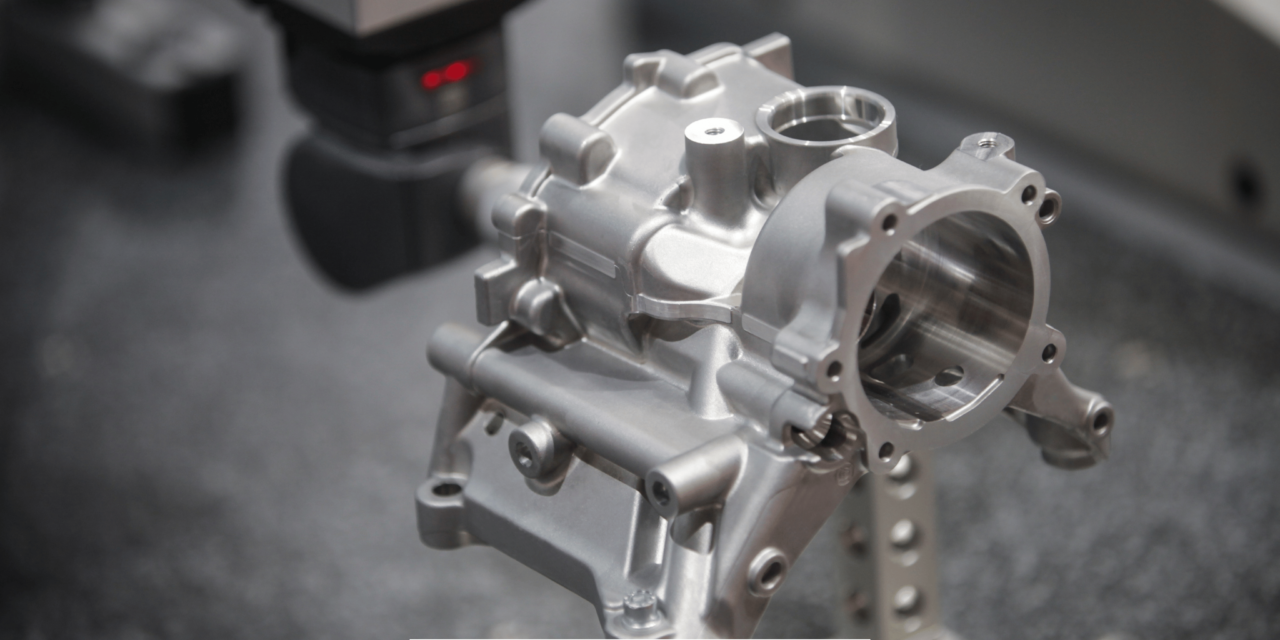
Introduction
Metal fabrication can be defined as the process of building structures from metals and from various kinds of raw metal materials. This is a complicated procedure used in multiple industries to manufacture end products, goods like auto parts, and structures like bridges and buildings, among others. Some of the expected standard metal fabrication processes and tools used mainly by the fabricators during this process include the following. In this article, the reader will be informed about six of the most popular metal fabrication processes.
Cutting
Even the most basic guide on how to use metals will not fail to include Cutting as one of the most basic yet essential processes. This may include the use of saws, shears, plasma cutters, water jets, lasers, and other tools to cut raw metal sheets and plates into the desired shapes and sizes.
Standard cutting tools include:
– Mechanical Saws: Chop saws, bandsaws and hacksaws are primarily used in cutting straight or curved edges on the material under consideration.
– Shears: Alligator shears, plate shears, ironworkers can cut straight through thick metal.
– Plasma Cutters: They are used in cutting metals during the process while at the same time giving a smooth finish on the edges.
– Waterjets: High pressure water jet and abrasives should be used for clean cuts without heat effects and it is recommended to apply it.
– Lasers: Provide accurately matched metal components and thin metal products for applications where high precision is needed.
Bending
Another vital metal forming process is bending where force is applied to curve or angle the metal.
Some ways metal is bent include:
– Press Brakes: Use punch/die male and female punch/die tools to perform accurate bends and folds.
– Rotary Benders: Twist cylindrical shaped parts to make helical coils and spirals.
– Rollers: Bend metal sheets through sets of rolls to create arches and cones.
– Slip Rolls: They are employed in bending round/tubular sections by gradually revolving metal around three rollers.
Joining
Joining techniques permanently fuse separate pieces of metal using processes like:
– Welding/Soldering: Welds metals with localized heat from oxyfuel or electric arc processes.
– Riveting: Defined by the use of metal or polymer rivet fasteners that are inserted through holes in order to fasten.
– Adhesives: There are some varieties of glue/epoxy which are designed to provide a firm hold on metal.
– Mechanical Fasteners: Bolts, screws and clips are the mechanical fasteners that can fix metal parts in a temporary manner.
Forming
With the application of pressure, bending alters the form of a metal substance through a process called forming without necessarily eradicating any substance.
This includes techniques like:
– Stamping: Uses large dies to force fit and shape blank metal sheets into the required parts for use in production.
– Forging: It is a process that employs localized heating and hammering or pressing to forge the metal.
– Rolling: Presses metal between two rollers and reduces its thickness by putting the metal through a number of pairs of rolls.
– Extrusion: Forces metal through a die opening to produce pieces of fixed cross-sectional areas.
Machining
Finishing or polishing of metallic components and parts through the use of various machines is essential in enhancing the shape and acquiring the right size of fabricated metal parts.
Milling, turning, drilling, and grinding are standard machining processes that use:
– Lathes: Turn parts to be faced, bored, knurled, or grooved against cutting tools.
– Milling Machines: Feed materials against a rotating cutter to slot, chamfer, gear-cut workpieces.
– Drill Presses: Employ rotating bits to drill holes and apertures in metals.
– Grinders: Use abrasives to polish and remove sharp edges and burrs on the surface of a machined part.
Finishing
Lastly, finishing processes add attractive protective coatings like paint, powder coatings, plating, anodizing, and more to fabricated metal parts using methods such as:
– Painting: Covers the surface with liquid paints that solidify/elize to provide color and protection from corrosion.
– Powder Coating: Like painting, but in this case, a colored powder is sprayed and then baked in an oven.
– Electroplating: Immerse the articles in the plating tanks and apply electric current to form layers of metals.
– Anodizing: It employs electrolysis to deposit an oxide layer on metals, such as aluminum, to enhance its toughness.
Conclusion
Concisely, it can be concluded that cutting, bending, joining, forming, machining, and finishing are six of the most important and most frequently utilized techniques for fabricating metal parts. Like other manufacturing processes, it is a skill that takes both training and practice to be able to fully and efficiently use the tools involved in these processes, but it is essential knowledge for metal fabricators. It is based on understanding these basic techniques that professional can bend metal into anything of their desire.