How Long Does The Sheet Metal Fabrication Process Take?
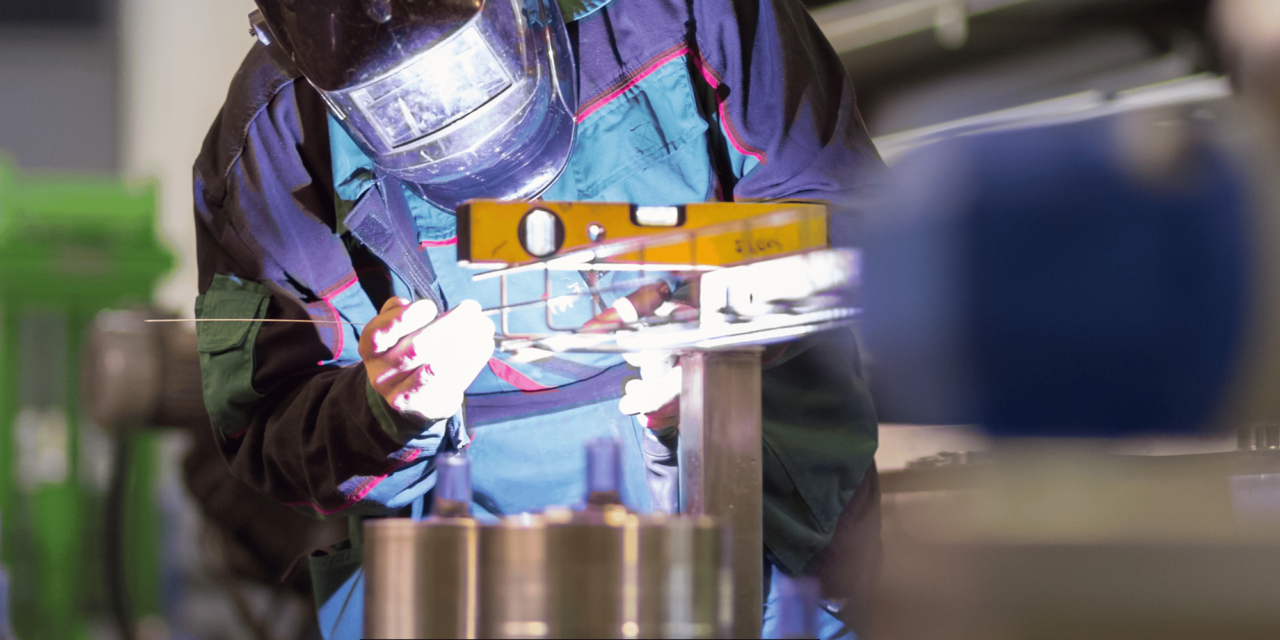
Introduction
Sheet metal working is manufacturing useful products like enclosures, racks, brackets, and the like from thin metal sheets through bending, cutting, and assembling processes which involve designing, tooling, cutting, shaping, welding, finishing, and forming. The total time taken to complete the analysis also depends on the size and the level of difficulty of the product. In general, an essential sheet metal part may take about three to five working days, while a complex one may take about two to three weeks.
Design and Tooling
The first method involves creating a product model with the correct specifications and then creating a model of the product on the computer using a CAD model. The design data generates the press toolings including the dies and punches to give the required forms to the sheets. When it comes to the creation of a new design, the tooling development takes usually within 1-2 weeks. When the design is existing or slightly changed, many of the tools used in developing the design can be reused, saving time.
Cutting the Metal Sheets
Once the blanking tools have been made, it is possible to stamp out the required shapes from metal sheets. This may take anything from a few hours to 2-3 days, depending on the sizes of the parts and the total quantity of the batch. CNC turret punch presses are used and are fast in operation. For very high production volumes, progressive stamping may be used.
Forming and Welding
The cut sheet metal pieces from the cutting operation are bent and formed on the press brake to get the required 3D shapes. Other parts might also by tack welded together. Small lots can be cut from flat sheets into finished forms within one day. In the case of large quantities, this step is done within one week at most is done at most.
Finishing
After being formed into the required parts, the sheet metal parts may be degreased and painted or coated as needed for the intended application of the product. This may entail sanding, buffing, or applying powder or wet coat. In many cases, simple finishing, such as cleaning or deburring of small lots, can be done in several hours. The surface coating batches should take about a week on average.
Hardware Addition
The final assembly is done in this section, whereby all additional hardware components not included in the initial build are installed.
Other components, including electronics, wires, motors, and fasteners, are then attached to the sheet metal enclosures and housings to form the end products. For simple products with fewer components, it can take a single day to do the final assembly. The final assembly of simple products with one or two sheet metal and hardware sub-assemblies may take about 3-5 days, while more complex products with many sheet metal and hardware sub-assemblies may take about 1-2 weeks in final assembly.
Quality Checks
Even at an intermediate stage, checks are made to ensure quality before the parts are transferred to the next level of fabrication. This takes a few hours after each of these main steps. The last process that is conducted on the products is testing and inspection. The units of simple items can take 1-2 days to undergo quality check, while the units of complex assembly components may take 3-5 days for quality check.
Summary
It is possible to produce simple sheet metal parts and products such as brackets and enclosures within one week. As for more detailed products such as machinery housings, furniture, complex medical equipment that comprises several formed parts and sub-assemblies, it may take 3-4 weeks in fabrication.
The sequence is as follows – Design and Tooling (1-2 weeks) > Cutting Metal Sheets (Hours to 3 days) > Forming and Welding (1-7 days) > Finishing (Hours to 1 week) > Final Assembly (1-2 weeks) along with Quality Assurance after each stage (1-5 days).
The total time is, therefore, the sum of time taken at each of the above-mentioned stages. With regard to simple sheet metal products, the total fabrication cycle may take between 1 to 2 weeks. The most complicated assemblies with stringent quality requirements can take about one to two months to complete.
Factors Affecting Time
Some of the critical factors that determine how long sheet metal fabrication takes are:
- Difficulty in product design
- The quantity of a product to be produced
- Number of Forming Operations Required
- Surface Finish Requirements
- Hardware and Assembly Integration
- Quality Standards to be Met
- Accessibility of Design Data/Tooling and Equipment
- Manual Operations vs Automation Level
Therefore, with these factors being optimized, sheet metal fabricators can reduce the fabrication time and supply products to the end user faster. Implementing newer technologies like CNC machines, 3D printing for tooling, and the integration of CAD/CAM software also aids in faster turnaround time on sheet metal products.
Conclusion
The sheet metal fabrication process involves cutting, forming, welding, finishing, and assembly operations, which may take a few days to a few weeks, depending on the product type, production quantities, and quality standards required. Basic structures can be achieved in 1-2 weeks, while intricate parts and assemblies can take up to 1-2 months. Through the proper choice of materials, fabrication processes, and fabrication resources, the fabricators can minimize the time taken to manufacture in order to be competitive.