Materials Suitable and Unsuitable for Laser Cutting
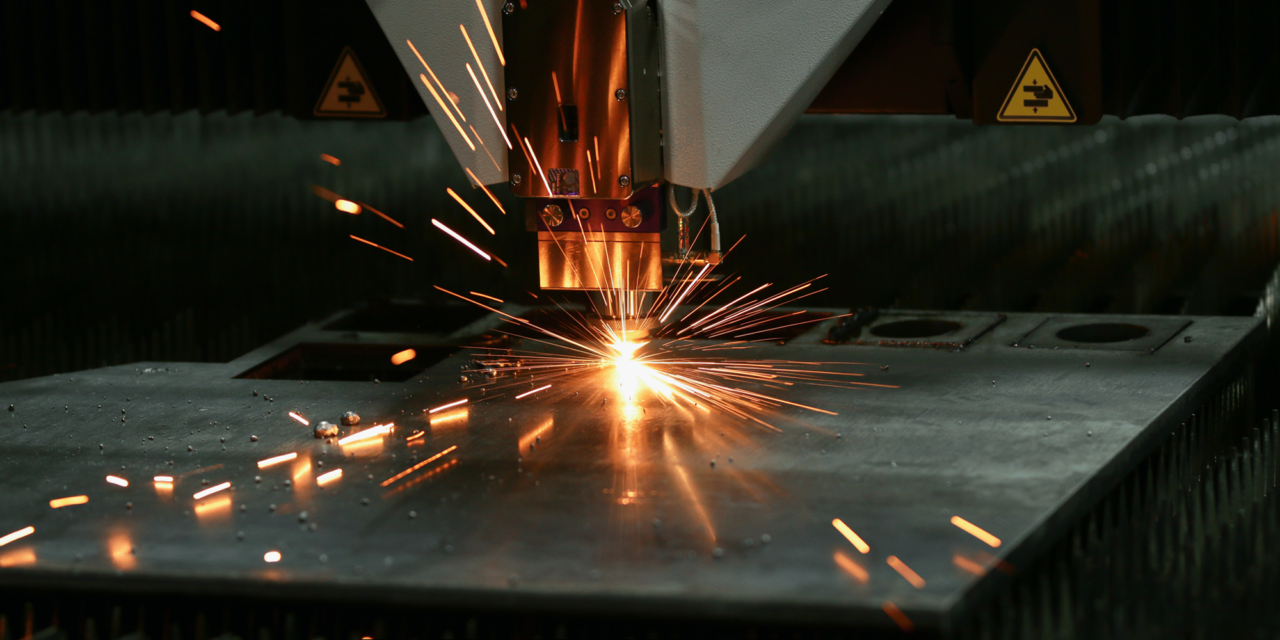
Appropriate Material for Laser Cutting
Many materials can be quickly and with excellent precision cut with the help of laser cutting technology.
The most commonly laser-cut materials include:
Metals
– Stainless Steel: Laser cutting is well suited to stainless steel due to its non-corrosive nature and high-quality surface finish. It provides a better edge finish and very sharp cutting. The fact that the material to be cut is highly reflective also makes cutting take a shorter time.
– Carbon Steel: Carbon steel, however, can also be laser cut, though it may need more energy than stainless steel. It offers a good edge quality.
– Aluminium: Laser cutting is a perfect process for cutting Aluminum. It uses less electricity to operate and has a lower melting point that enables faster and cleaner cuts.
– Titanium: While cutting titanium, high power is needed for laser cutting, giving very high edge quality cuts.
– Brass and Copper: Brass and copper materials are thermally conductive and enable accurate and thin laser cutting. The cut edge has high reactivity with oxygen; it should be cleared immediately after cutting has been done.
Plastics
– Acrylic: Laser cutting is also ideal for acrylic because of the material’s characteristics. It evaporates with little residue, and has a flame polished edge to it.
– Polycarbonate: It will not melt around the cut lines or become stiff and gummy, making it easy to cut through polycarbonate. It provides a high and accurate finish cutting.
Wood and Paper
– Plywood: Plywood is also one of the best materials that can be worked on through laser cutting. It barks the wood somewhat, but it can carve more detailed designs precisely.
– Cardboard and Paper: Thin sheet materials like cardboard, paper, etc. can also be cut using laser, for instance, for the creation of packaging mock-ups and models.
Fabrics
– Natural Fabrics: Garments such as, cotton, wool, leather, etc. can be easily cut by laser. Low melting point materials such as synthetic material polyester are not appropriate.
Conditions that make a material fit for laser cutting.
The suitability of a material for laser cutting depends on factors like:
– Composition: The uniform density and nature of plastics and woods are preferable to others since they have a constant and consistent nature when cut.
– Melting Point: Substances that have low melting points change to vapor when the laser broils them. This results in clean and accurate incisions as opposed to the edges melting into each other and becoming blurred.
– Flammability: Highly flammable substances such as wood or plastics do not yield good cut quality as materials that are hard to ignite, like metals.
– Reflectivity: In other words, some materials such as aluminium and copper are reflective, hence they are easier to cut than other non-reflective materials such as acrylic.
– Thickness: Laser cutting is more suitable for thin sheets. Thick sheets may need to be passed through the cutter a number of times or precut in some way.
What are the types of material that are not suitable for Laser Cutting?
Although lasers are versatile and can cut through virtually any type of material, there are certain materials that are either more challenging to cut with a laser or should not be cut with lasers.
These include:
Metals
– Tool Steel: Tool steels are usually heat treated and are too complex to result in clean laser cutting. Cuts have bad edge condition with thermal cracks.
– Lead: Lead is a relatively low melting point material and it decomposes under influence of laser cutting rather than evaporates. This results in rough edges with debris.
Plastics
– PVC: Yet, PVC releases toxic chlorine gas when heated or when burned, which has far-reaching environmental implications. This makes PVC a risky material for indoor laser cutting.
– Nylon: Nylon undergoes melting and burning instead of vaporization during laser cutting, and for this reason does not offer quality edges.
Other Materials
– Glass: The material of glass undergoes thermal shock and stress of laser cutting and as a result cracks. The cut edge is irregular and not a clean edge.
– Ceramics: Ceramics do not melt when exposed to lasers, meaning that there is restricted material removal. They also appear along the cut lines.
– Composite Materials: When cutting through non-homogenous composites with multiple layers of different materials, the composite may delaminate or crack.
Conditions That Make a Material Inadaptable for Laser Cutting
Properties that make materials perform poorly during laser cutting include:
– Thermal Cracking: Materials such as tool steel and glass tend to crack when subjected to heat, such as thermal cutting, and degrade during laser cutting rather than vaporizing.
– Toxic/Irritant Byproducts: Some of the products such as PVC emit hazardous gases when exposed to heat. These toxic byproducts make the materials dangerous significantly when cutting them within the enclosed space.
– Excessive Melting: Substances that soften but do not vaporize at the laser interface leave behind a poor-quality edge with congealed material and debris buildup.
– Inhomogeneous Composition: Different density, composition and layers structure of composite materials result in low quality and uneven laser cut.
Conclusion
According to the type of laser used, it is possible to cut metals, plastics, fabrics, and many other materials with high precision. Precision and cut quality depend on the use of materials that suit the machine in terms of the thermal characteristics, melting points, and the mixture used in the material. The materials that should not be used for laser cutting include those that are likely to crack, melt, or emit toxic fumes for the sake of safety and efficiency. With these aspects in mind, the capability of laser cutting can be harnessed for fast construction.