Sheet Metal Bending – Methods, Design Tips & K Factor
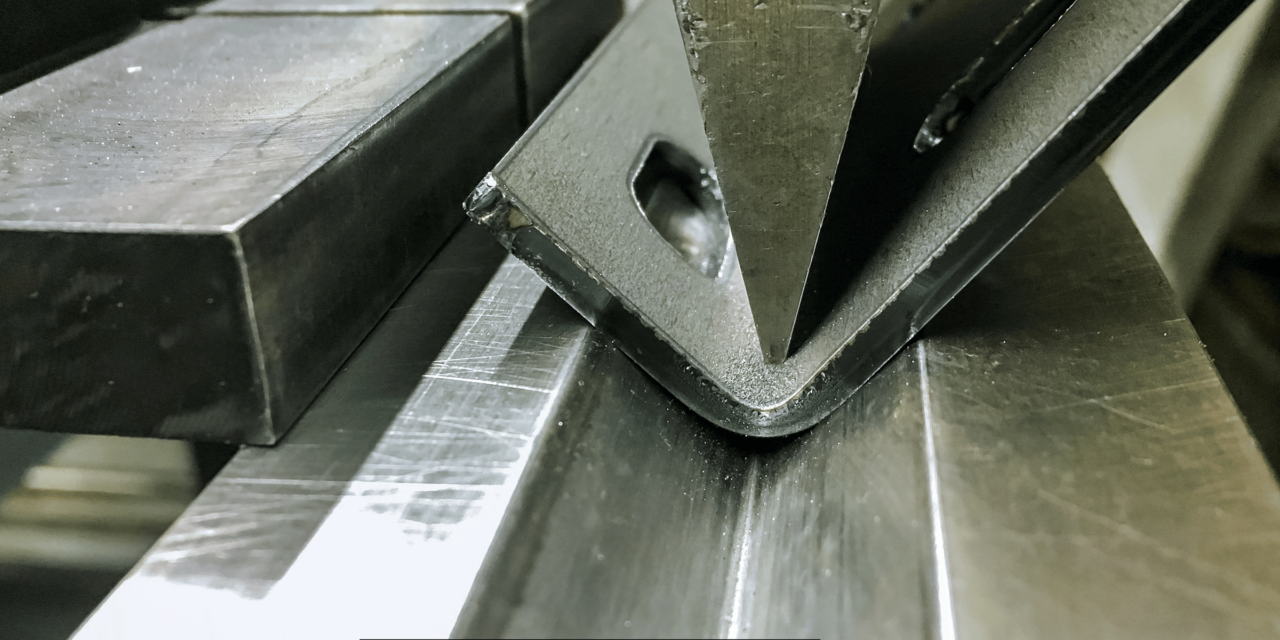
Sheet Metal Bending Methods
Sheets can be bent in various manners to form the required shape and size, and some of these procedures include standard bending methods:
Press Brake Bending
– The most widely used bending technique that occurs when the shape of the punch and die set is adjusted on a press brake machine. It enables one to get a high level of accuracy of the bend and the amount of control one desires to have.
Rotary Bending
The rotary bender machine rotates the sheet metal to bend it to form cylinders and curved shapes in the material. Simple but limited shapes.
Roll Bending
– Sheet metal is fed into pyramid style set of roller that gradually form the metal into a pre-set tight curvature. Found in rolling tubes and cylinders only.
V Bending
– This die is in a V-shape; it is applied in shaping angle bends and channels from sheet metal. There is no need to create a bottom die.
Air Bending
– It is pretty similar to press brake bending. Still, the die is open at the bottom to allow for the bending of particular shapes only. It creates sharper angles than press brake bending while creating angles that are less precise.
Design Considerations for Sheet Metal Bending:
There are various factors involved when designing a sheet metal bending. These considerations help determine the feasibility and control the outcome of the bending process:
Bend Radius
– It implies that the force decreases when the circle radius increases. In contrast, it increases when the radius decreases. This means that thicker metals and work-hardening alloys will need higher bend radii.
Bend Deduction
– The two axes of the cross-section are neutral, and their length increases during bending, which means more material length is added.
Spring back
– This is the behavior of a bent metal with a slight tendency to return to its original state from the bent position. Some of these are absent; the amount must be compensated in the die design.
Direction of Bending
– The referenced metals are arguably stiffer, and their properties vary with the orientation of grains. It may require testing.
Inside Setback
– When it comes to complex shapes with more than one bend, the position of the first bends affects the following bends. Therefore, the sequence and design of these images are essential.
The application of K-Factor in Sheet Metal Bending
The K-factor is a value that is utilized in the process of bending and stamping sheet metals. It assists in calculating the bend deduction and the minimum punch radius that is required to create a specified radius on a given piece of sheet metal.
The K-factor is derived from these parameters:
– The tensile strength of the particular material being used.
– Overall percentage increase in the length of the material
– Percentage reduction in thickness of the neutral axis
– Inside bend radius
This indicates a lower K-factor, which translates to reduced force that is applied to both the punch and die during the bending process. This makes it possible to use narrow tools, which are cheaper compared to using a more comprehensive tool. K-factor ranges between 0. 3 and 0. 5 and is generally favored.
The K-factor governs what minimum punch radius can be used with a particular material thickness. That is why it is inadvisable to use a radius that is too tight, as it can crack the metal. It should be emphasized that consulting manufacturer bend radius tables is always advisable.
In the case of a 90-degree bend, the bend deduction is directly obtained using the formula K-factor x metal thickness x K-factor.
Achieving this involves the use of test samples of sheet metal to adjust the value of the K factor. There is no complex software to ‘predict’ bending behavior, which helps optimize the design of pipes.
Conclusion
Sheet metal bending is a beneficial manufacturing process, and it allows for the easy formation of several shapes and end products. You will learn some of the most important factors surrounding the design of the sheet metal part, the tools that will be used in bending the part, and the material properties to ensure that the bending of the sheet metal part is practical. Thus, specifying factors, which include the bend radius, the deduction, spring back, and K-factor, is necessary to achieve accurate, flawless bends. As with any advanced software, it also enhances accuracy in solving problems and lessens dependence on guesswork.