Fiber Laser Cutting vs. Traditional Sheet Metal Cutting
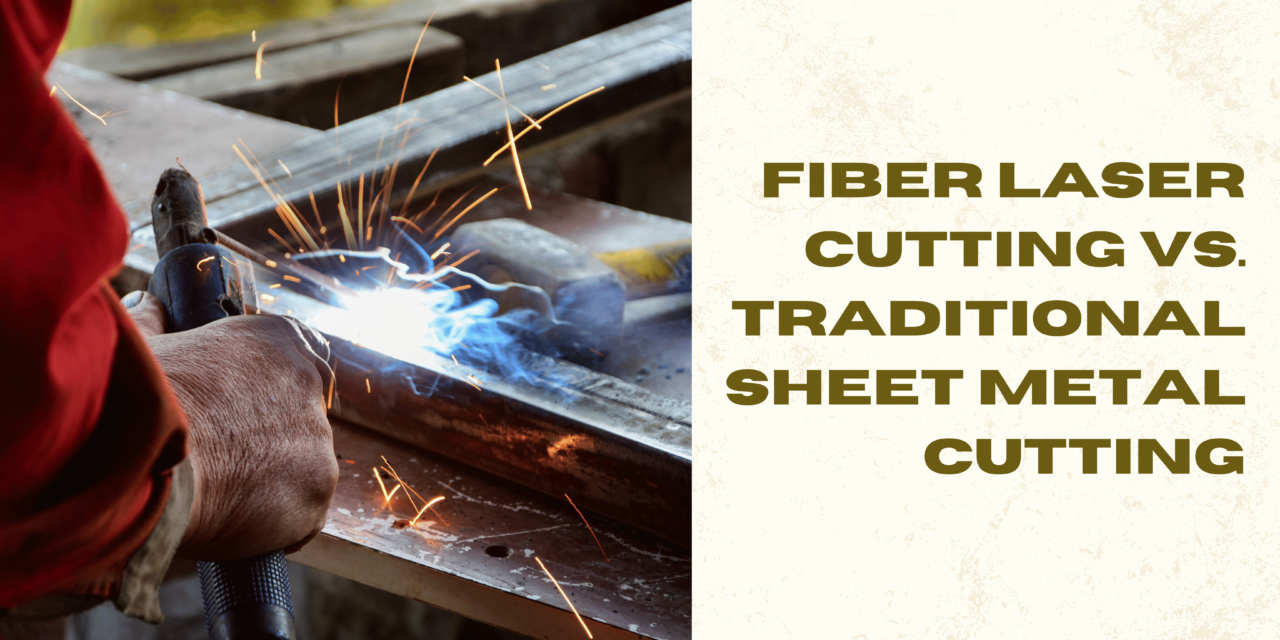
Fiber laser cutting is a process that employs fiber lasers to cut materials, especially metals like steel, aluminum, and copper, with high precision.
Fiber laser cutting is a thermal cutting process that does not involve physical contact with the material being cut. The process consists of the use of a high-power density laser beam that is used in the melting of thin metals. It involves using a laser, which is produced through a process known as stimulated emission of electromagnetic radiation and passed through an optical fiber to the cutting head.
Fiber laser cutting brings several benefits when compared to more traditional types of cutting techniques:
High Cutting Speeds
Another significant benefit of fiber lasers is that they have the potential to make swift cuts in many instances, far faster than many mechanical cutting methods. This has made it possible for the cutting speeds to go up to 25 meters per minute. This makes it possible to achieve high production and performance rates in the manufacturing industry.
Precision and Accuracy
Fiber laser cuts with greater accuracy and has a very thin kerf, but the cutting speed is comparatively slow. The width of the laser beam is extremely narrow, which allows for high-detail work and contour cutting of 0. 1mm; this minimizes post-processing.
Low Running Costs
The running cost of fiber laser cutting machines is relatively low compared to the mechanical cutting processes. It has no tool wear; it doesn’t need any lubricants or coolants. Thus, the only maintenance that may be required is regular maintenance.
Cutting Capabilities
Using the highly focused laser beam, it is possible to work with sheets of different thicknesses, starting with very thin foils to stainless steel with a thickness of up to 25 mm. It can make cuts in all conductive metals or materials that have the conductivity of electricity.
High-Quality Cuts
Fiber laser cutting has many advantages; firstly, the cuts it makes are accurately precise, with smooth edges and clear details. This helps to minimize the need for cleanup of edges after cutting has taken place.
Traditional sheet metal cutting is the process of cutting a flat metal into a required shape using tools such as chisels and hammers.
Conventional cutting means manual cutting of sheet metal using mechanical tools as opposed to new-age techniques that involve lasers or water jets.
The most common mechanical cutting processes are:
- Sharing
- Punching
- Sawing
This process involves the use of mechanical cutting tools like cutting blades, punch and die sets, and saw blades to cut sheet metal.
Advantages of Mechanical Cutting
Established Technologies
Flame and plasma-cutting equipment are technologies that have been around for quite some time and are not necessarily new technologies that would require an investment in new equipment by many shops. As you can see, no new investments in new equipment are needed.
Cuts Non-Metal Materials
Mechanical cutting is one of the advantages of the method; it can cut materials that do not lend themselves to laser cutting, such as plastics and wood. Laser cutting is a process where materials are cut by a focused laser beam, and only materials that can be influenced by the focused laser beam can be cut by lasers.
No Heat Affected Zone
In mechanical cutting processes, no heat is transformed to the parts that are being cut, so the parts are accessible from heat-affected zones. It is also important to note that some of the material, when laser cut, will have an area that has been affected by heat and will, therefore, alter some of its characteristics.
Lower Equipment Costs
In general, everything required for mechanical cutting, tools, equipment, and machines is much cheaper to acquire than laser cutting machines.
Disadvantages of Mechanical Cutting
Slower Cutting Speeds
The cutting speed of mechanical cutting is comparatively slower than that of laser, which can significantly reduce productivity and throughput. When parts are complex, they take longer to produce, and this is attributed to the fact that the production involves a combination of several small and intricate parts.
Limited Cutting Capabilities
Shearing and punching have relatively low thickness, which is around 10mm cutting capacity. The thickness acceptable for cutting is, however, lower than that of lasers.
Lower Precision
Another limitation of mechanical cutting compared to laser cutting is that mechanical cutting is relatively less precise as it is not as accurate as laser cutting. This is primarily due to the mechanical methods that can only have an accuracy of about 0. 5 mm.
Tool Wear and Maintenance
The tool costs are high after using it for some time due to the effect of wear. Like any other equipment, tooling needs to be maintained and sharpened periodically to achieve optimum results. There is always a breakage, which may lead to more time required for production.
For many shops, the use of the fiber laser cutting in addition to those mechanical method is considered to be a two technology strategy that takes into consideration the potential for speed, flexibility and cost. The laser is the most suitable for delicate, accurate and fast cutting and this makes mechanical cutting ideal for cutting through thicker materials or non-metals. This makes it possible for shops to achieve better competition levels and thereby be able to handle different tasks.