How Metal Fabrication Improves Product Prototyping
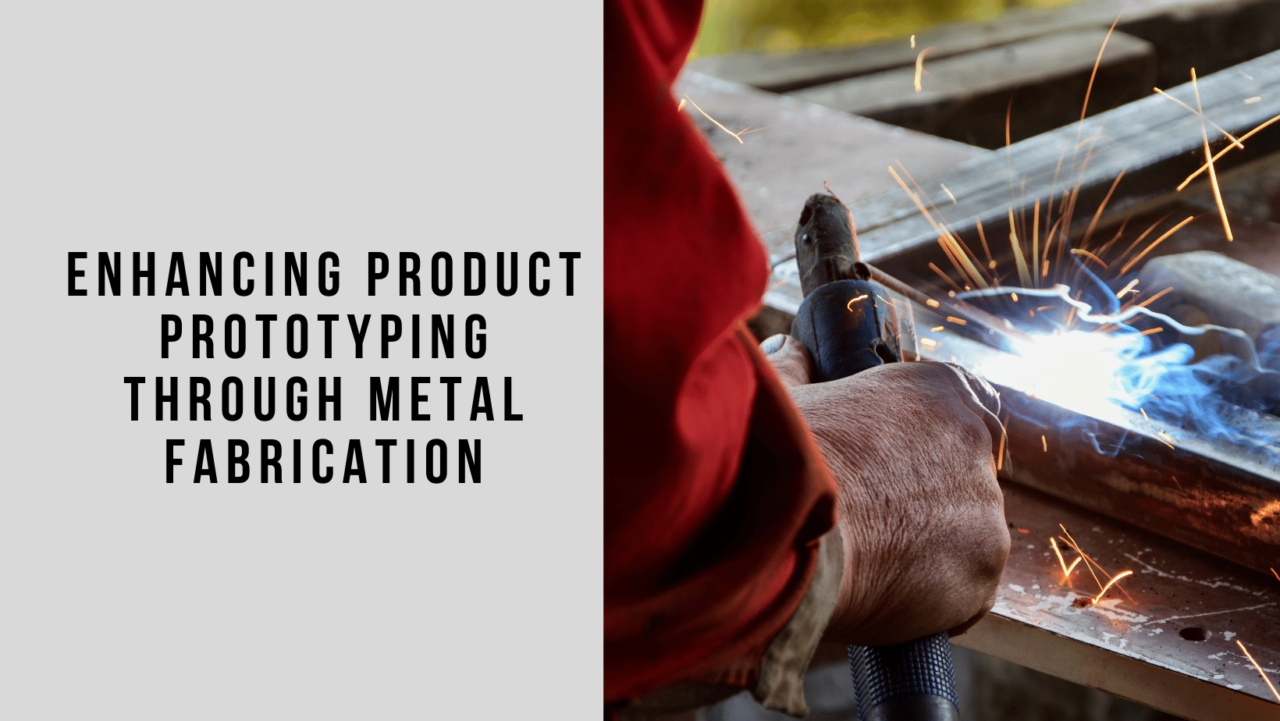
Accelerating Concept Testing
Technologies such as CNC machining, laser cutting, and sheet metal fabrication can quickly convert digital model designs into actual physical arrangements. This makes it possible to conduct concept testing very early in the design process, thus enabling the designer to test various concepts before bringing in the technical experts to work on them.
Some of the key benefits include:
Faster Design Iterations
This way, designers can get a feeling of a concept in metal, at least a part of it, in a matter of days or weeks as opposed to months. This, in turn, helps in the faster development of subsequent design revisions.
Catch Issues Sooner
This means that instead of discovering that there is a design problem, it is done before the fabrication process, hence saving users a lot of cash in the process.
Informed Design Decisions
Prototyping helps to make better decisions regarding materials and color schemes, as well as knobs and buttons and other elements, before finalizing the design.
Reducing Prototype Expenses
Blending the use of these superior metal fabrication technologies with the small-batch manufacturing approach makes it possible to design prototypes within a shorter time and at a lower cost compared to conventional manufacturing processes.
Enabling Functional Prototypes
Besides visual prototypes used in concept modeling, metal fabrication enables highly functional prototypes at a later stage in the design process, such as functional models that are used for testing and verification. Some of the functional activities that can be done include machining, casting, stamping, and more in creating functional metal prototypes.
Accelerating Testing & Validation
Metal fabrication produces first samples that have the same characteristics as finished production parts in terms of strength, durability, and accuracy. This also assists in quickening the onset of test and validation procedures from design verification to field testing.
Streamlining Approvals & Production
Also, prototypes help internal teams, stakeholders, regulatory bodies, and consumers to understand the final product before the manufacturing process. This makes the approval and production processes much easier to achieve.
Main Metal Fabrication Processes in Prototyping
There are versatile prototyping methods in metal fabrication to suit prototype requirements in terms of material, number of prototypes that need to be produced as well as the complexity and accuracy of the prototypes.
Here are some of the most widely used organizational communication methods:
CNC Machining
CNC machining is typically preferred for its accuracy and the ability to achieve high-quality surface finishes. Machining processes such as milling, turning, drilling, and tapping make it feasible to manufacture up to thousands of metal components in aluminum, steel, titanium, etc. Ideal for functional prototypes.
Sheet Metal Fabrication
Laser cutting and CNC punching provide professional cuts on sheet metal while bending and welding assemble enclosures, racks, chassis & others. Perfect for concept models and structural prototypes as they do not require the functional properties of a concrete part.
Casting
Die casting and sand casting are processes through which metal parts are made by using molds and filling them with molten metal. Casting provides a means for producing larger volumes for later stages of testing. Other materials that can be casted include the aluminum, magnesium, and steel among many others.
Rapid Prototyping
Some of the additive techniques, which lay down material successively to build up the object over its computer aided designs (CAD) include direct metal laser sintering (DMLS) that builds prototypes from metal powders by heating them to create layers based on an STL file. Geometry is not limited to simple shapes but could be highly complicated.
Metal fabrication for prototyping has the following advantages:
Accurate Replication of Specs
Tolerances refer to standards that help determine how closely metal fabrication aligns with the specific needs of a final production part.
Wide Range of Materials
Almost any metallic material including stainless steel to copper to the complicated metal alloys used in the aerospace industry can be fabricated to provide material integrity.
Complex Geometries
Modern metals require less thickness and more detail, making it easier for machines to create complex shapes that are not possible with essential tools.
Appearance & Feel
Through polishing and finishing processes, the fabricated prototypes of the metal can resemble the look and feel of the final product.
Speed & Agility
When it comes to rapid turnaround on prototypes, metal fabrication can be relied upon to ensure that product development continues at a fast pace. However, priority services with a rush delivery option are available.
Conclusion
It is also important to point out that using metal fabrication to the greatest extent possible and starting it as early as possible in the product development cycle brings enormous gains in the creation of prototypes. The extraordinary precise, performance and velocities enable prototypes that facilitate in fast track concept validation, minimize risk, control cost, ease the approval process and ensures manufacturing readiness. Indeed metal fabrication is an area that should receive a lot of attention because the rewards that come with it are enormous especially if your product has metal parts.