Laser Metal Cutting – Key Advantages And Characteristics
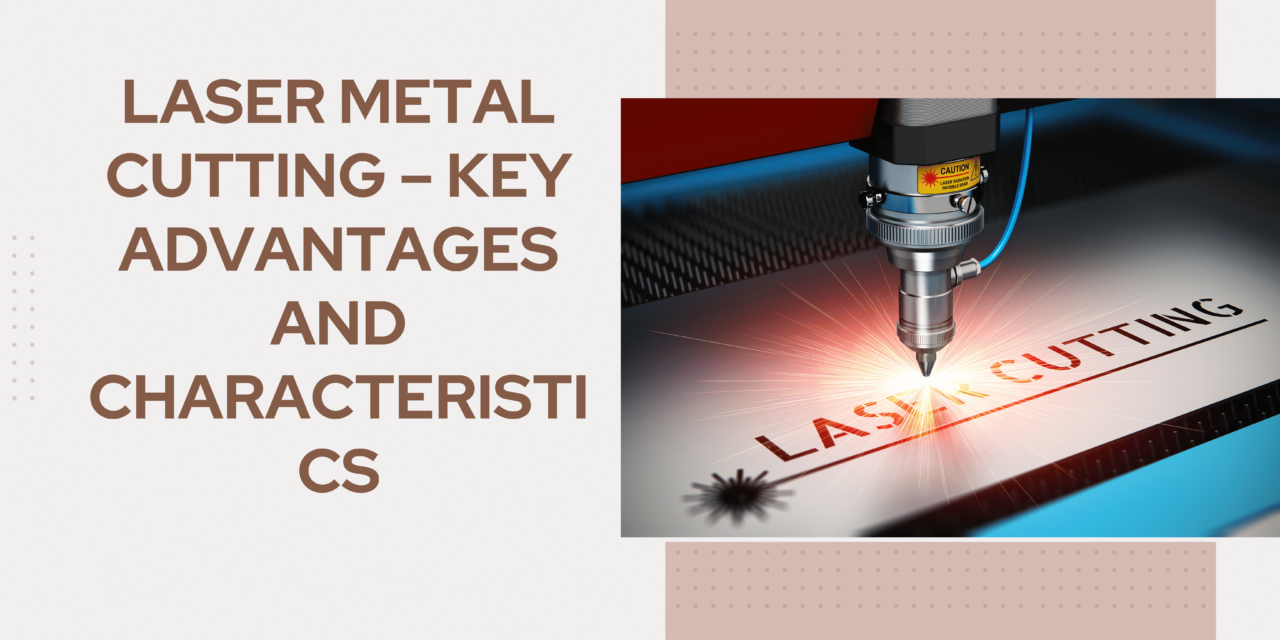
While compared with plasma or oxy-fuel cutting, laser cutting does have some unique advantages and function characteristics that make laser cutting a flexible, highly efficient, and effective cutting technique for metals. This article will discuss and describe laser metal cutting technology in terms of some of its significant advantages and features.
Speed and Precision
High-speed cutting is another benefit of laser metal cutting because laser cutting is exact and accurate even when working at a very high speed. Today’s industrial lasers are high-powered and can cut thick steel plates at a rate of more than a hundred inches in a minute.
This speed is significantly higher than that of the manual cutting methods that can be employed when using cutters. It also outperforms the speed of rival technologies, including CNC machining or plasma cutting. From the analysis of its features, the high cutting speeds help reduce production time and increase workflow.
Another advantage of laser cutting is that it affordably has high cutting speeds and high precision when cutting materials. The laser can also be focused on petite spot sizes, enabling high-accuracy cuts, complicated shapes and designs, small holes, and openings to be made accurately and within small tolerances. Since the cutting head vibrates continuously, accuracy within one-thousandth of an inch is achievable. This makes lasers capable of cutting more intricate parts that may be difficult to work on by other methods.
Cut Quality and Edge Finish
Laser cutting is less invasive than other thermal cutting methods, with the heat-affected zone and slag or dross formation reduced considerably. This results in sharp cuts with smooth edges that do not require much refining and finishing compared to other methods.
The laser beam is far more focused than the flame to deliver an intense burst of energy to scale material up instead of melting it. This implies less distortion, warping, or adverse changes to the original material surrounding it. These high-quality cuts involve very little post-processing, like deburring or grinding. Typically, edge finishing is not very sharp. It can be readily welded or powder-coated without further refinishing.
Material Compatibility
Most laser machines can cut various ordinary engineering metals such as mild steel, stainless steel, aluminum, brass, copper, and others. The flexibility of laser power and speed in cutting also implies that a large variety of material thicknesses can be worked on, ranging from sheet metal to thick steel plate 1” or more.
Some materials that can be cut using this method include flat stock, round tubing, rectangular structural profiles, pipes, and metal grating or mesh. For these reasons, the technology is well suited to the needs of many industries since it has the capability of cutting through many types of metals. This ranges from simple manufacturing equipment to food processing equipment to pharmaceuticals equipment and aerospace components.
Cut Geometry Flexibility
The cutting head of the laser cutter is computer numerically controlled (CNC), so the laser can be directed along any path that is possible, making it highly versatile in terms of the shapes it can cut. Regular cuts, tapering, piercing, profiling, bending, angles and, grooving and other specific shapes can be cut through the help of laser cutting machine.
Cutting tool is not a constrain on the parts with multiple geometries or holes when they are subjected to laser cutting. It is also essential that no secondary operations are needed for the completion of specialty features in many cases. This also ensures a good nesting of parts and a shallow extent of wastage on scrap material.
Low Running Costs
Subsequent to acquiring an industrial laser cutter, the direct cutting costs are usually considerably lower than those of other methods, such as machining or water jetting. There are no consumables required as in plasma cutting, and the costs for these consumables are significantly low. For the process of ejecting the molten material nitrogen or compressed air is utilized as the assist gas.
Operating costs are defined in terms of electrical energy consumption, maintenance processes, and replacement of minor wearing spares during operation. However, the subsequent increases in cutting speeds and high usage of the machine on average per part make the unit cost extremely low. This makes lasers perfect to be adopted in volume manufacturing.
Automated Operation
Contemporary laser cutting machines include elements of automating the process of loading and unloading sheet metal. This leads to a minimal optimum direct labor input once jobs are programmed in this production process. Several sheets can be set up on the machine with others waiting for their turn, and the process can be left to run automatically. Suppliers are only required to be supplied with raw materials, which they then process and distribute on a repeated basis.
In conjunction with the programming by importing files from CAD and automatic compensation of precision, laser cutting is a highly efficient, fully automated type of fabrication. From the view of human resources, the demand for labor is significantly lower than all other similar products. This increases efficiency and reduces the costs relating to direct cutting labor.
Conclusion
Laser cutting has many benefits as it provides desired precision and speed and offers high-quality cuts; lasers are also versatile as they can cut a wide range of materials and use flexible cutting paths. It is one of the most advanced technologies for the metal fabrication industry of the present day. The need for minimal manual intervention and low cost per part also makes industrial laser cutting systems one of the most efficient metal cutting solution.
Higher power lasers and enhancements of the machine tools are the reasons for the increased speed, performance and accuracy in the future. This will firmly establish laser cutting as an indispensable solution for sheet metal working and precision metal cutting, which would apply to almost every industry.