8 Welding System Anti-Aging Tips
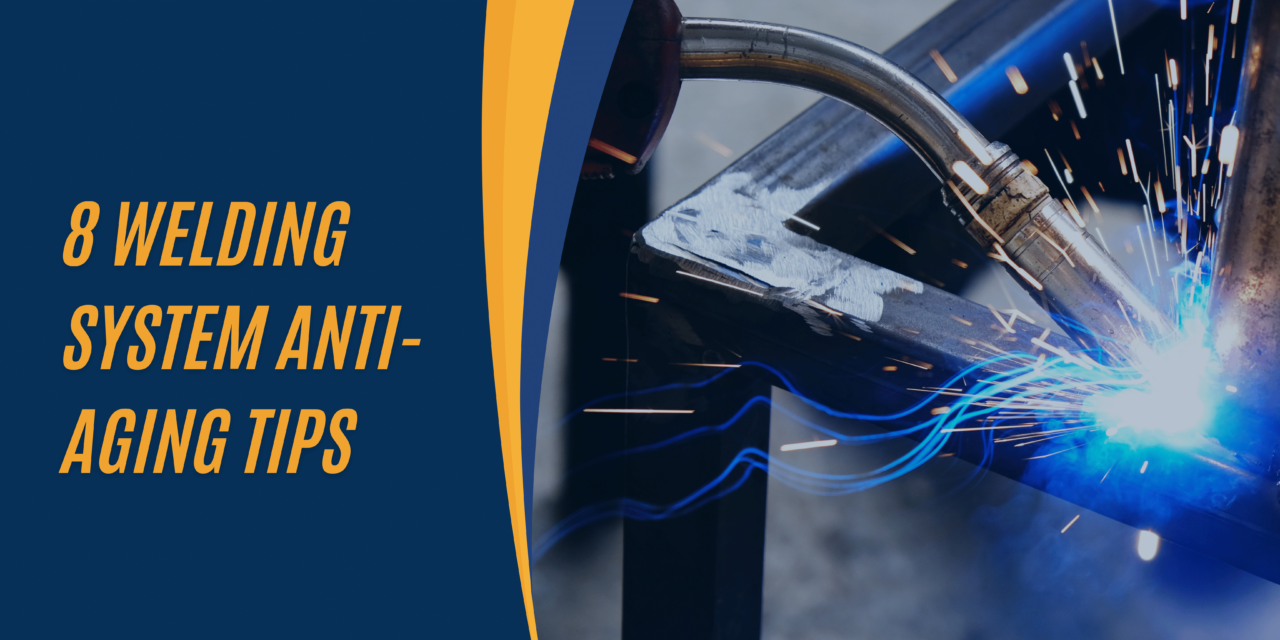
Welding equipment is exposed to the temperature, spatter, mechanical overload, and strain during ordinary usage. The mentioned factors can seriously impact the efficiency of your welding system within no time. Regular preventative maintenance and care will protect and prolong the life cycle of your welding equipment as well as grounds for premature breakdowns and failures. Here are eight tips to keep your welding system operating like new for longer: Here are eight tips to keep your welding system operating like new for longer:
Perform Regular Cleanings
* The dirty welding torch and wire feed system need to be wiped regularly with compressed air and a wire brush to remove rust from it.
* Swept out any debris hidden in cable lines duct
* Wipe with a clean cloth to remove stains from the outside to avoid residue forming.
Replace Consumable Parts
* Follow the manufacturer’s guidelines in terms of the items to be replaced at regular intervals in order to limit the effects of wear and ensure good welding performance.
* Perform drive roll inspections when grooves are present, or the rolls are no longer able to control the wire production.
* Replace cables if cores become visible through the dielectric or insulation frays around it.
Lubricate Moving Parts
* In order to enhance the welding areas with sliding parts, use a grease designed especially for welding parts on these surfaces.
* Lubricate wire guide rods, drives, and bearings, as well as tensioner rolls.
* Greasing torch necks with an appropriate lubrication agent to ease their articulations.
Protect Gas Hoses and Regulators
* For gas hoses, try hanging them vertically or coiling them loosely when not using them, thus preventing the bending of pipelines.
*Make sure that hoses and regulators are clear from sparks, spatter, and open flames during welding
* Therefore, it contributes to frequent checking of the existence of leaks and quick replacement of hoses or regulators that are in bad shape.
Monitor Cooling Systems
* For water-cooled torches, investigate another step of hoses and tubes for cracks or holes and change immediately if something is found.
* According to the manufacturer’s recommendations, use up-to-date procedures to drain, flush, and refill coolant.
* Make sure that coolant flow stays uninterrupted and offers adequate cooling.
Inspect Power Connections
* Make sure you look for hot plugs, sockets, and links in all locations.
* Get rid of the looseness of the connections quickly so that the arced damage can be avoided.
* If the male plugs are melted or deteriorated, change them to new electrodes.
Store Properly When Not in Use
* Wrap the welding machine, wire feeder, and all the auxiliary equipment under the sheltered with the cover when not welding.
* Hand welding kits, cables, lines and guns upwards on wall hooks for an easier access.
Keep all items in unique places free of moisture, terrible shocks and close to environmental temperature. Make sure that they are safe from the effects of vibration and stomping.
Schedule Preventative Maintenance
* Organize regular maintenance slots based on documented work hours.
*Qualified staff can competently diagnose and carry out comprehensive inspections and part replacements.
* Preventing maintenance ensures safety, increases the number of working years, and helps avoid unplanned stops.
Performing these simple cleanups, checks, and maintenance of your welding equipment requires little time or energy yet roundabout short-term benefits. Your weldment remains alternatively longer life, do the job better, and just need repairs less when you are ready to use system maintenance. You can save time and money by focusing on some easy anti-corrosion measures now so that you can keep all your welding machinery functioning well for many years.