5 Industrial Fabrication Welding Service Types
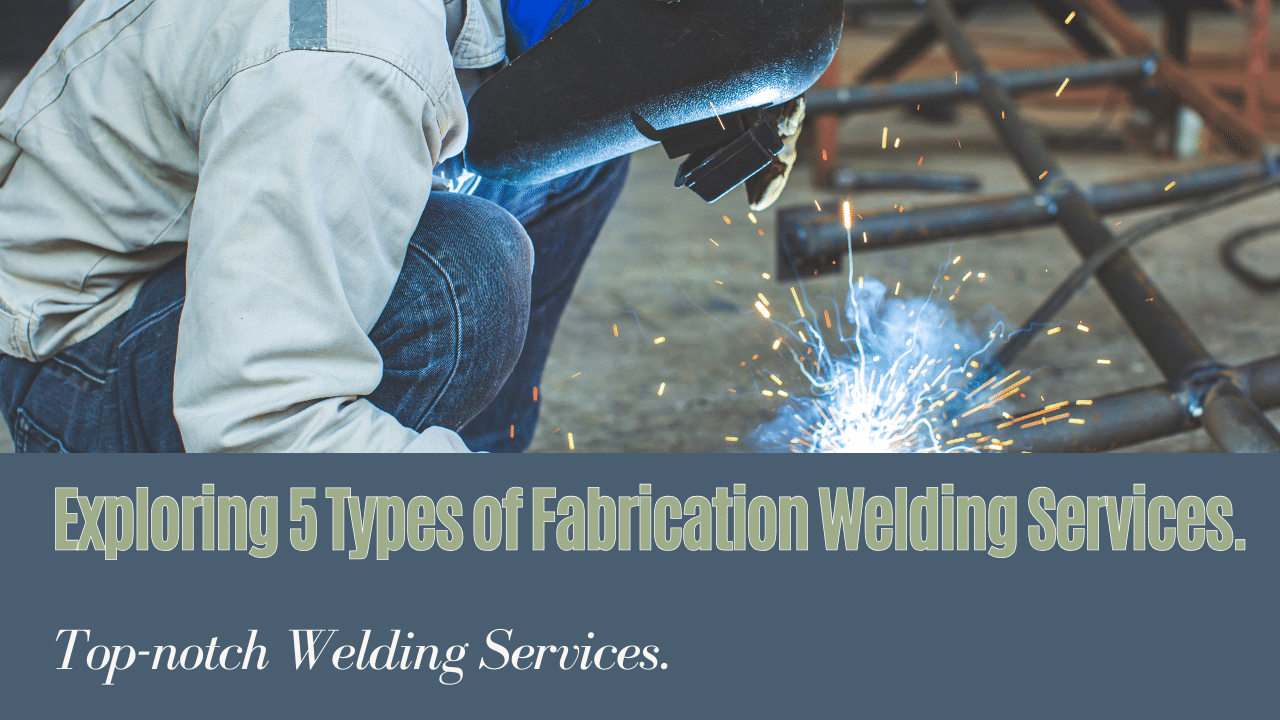
Introduction
Industrial metal fabrication for the machinery that help assemble metal components to make large structures – or overall products. In the majority of fabrication projects, welding is a very crucial operation, and there are numerous welding technologies concurrently existing in the industrial applications; each one is being used for a specific purpose. Here, the article will briefly describe the five most prevalent types of welding that are commonly requested in industrial fabrication.
MIG Welding
MIG(Metal Inert Gas) welding or GMAW (Gas Metal Arc Welding) is one of the most common as well as very flexible types of welding techniques used in welding industrial fabrication. It includes a replaceable wire electrode that slides through a welding torch also accompanied by an inert gas (shielding) that creates the arc for welding. Some of the benefits of MIG welding include: Some of the benefits of MIG welding include:
High Deposition Rates: You have to use much higher heat and speed than the processes, say, arc welding, for instance. This improves productivity.
Ease of Use: MIG welding is more accessible to acquire and employ as compared to other welding types.
Versatility: Welding various components like thin sheets and heavy pieces can be done smoothly with the same MIG welder. Its suitability for working with several metals, such as mild steel, stainless steel, and aluminum, cannot be denied.
As a result, MIG welding is used in the production of spare parts, storage tanks, pipeline systems, pipes, and structural frames.
TIG Welding
TIG (Tungsten Inert Gas) welding relies on a non-consumable tungsten electrode with an inert shielding gas to generate the arc. Some benefits of TIG welding: TIG (Tungsten Inert Gas) welding relies on a non-consumable tungsten electrode with an inert shielding gas to create the arc. Some benefits of TIG welding:
High-Quality Welds: High-efficiency TIG (Tungsten Inert Gas) allows for the formation of pure, solid, and uniform welds with excellent metallurgical properties. This is going to be fundamentally important, especially for critical things.
Ideal for Thin and Difficult Materials: The narrow heat beam gives you opportunity to weld stainless steel, aluminum, magnesium, copper and metals that are difficult to work with as thin plane.
Precise Control: In comparison to other welding process type, TIG offers welder a better control over the welding variables thus resulting in very precise welds.
The improved control and tacking ability are vital reasons why TIG welding is widely used in the high-end fabrication of aircrafts, spaceships, nuclear components, bicycle frames, and precision medical apparatus are only but a few examples.
Stick Welding
In shielded metal arc welding (sticking weld), the flux coated consumable electrode is used for the production of the weld. Benefits include:
Portability: The cost of the stick welding machines and portability make them a preferred option. In addition, they allow you to work indoors and outdoors as opposed to MIG/TIG alternative.
Versatility: You’ll be exposed to welding many types of iron and non-iron metals using different single or multi-component electrodes. When compared with stainless steel, high carbon steels and nickel alloys can all be stick welded or arc welded.
Minimal Surface Preparation: Stick welding can be used to weld joints in which a lot of oxides, paint and dirt are present as for other welding processes. A rougher surface than average comes often is enough.
Consequently, stick welding is still a top choice, because of its favorable conditions, in the fields of industrial fabrication, involving structural steels, storage tanks, fixing machineries, repair and maintenance applications among others.
Laser Beam Welding
The focused high-power energy of a coherent laser beam is concentrated on a tiny area of the parts to be bonded. Benefits are:
Extreme Precision: Laser welding is narrow and deep within the competence of 0.5mm without inferiority to other methods for high precision.
Minimal Heat Input: The laser energy is practically absorbed at a small part which is why heat distortion of component is not an issue.
High Speed: The speed of laser welding can be achieved at 100 m/min or more and even more, which is highly far outstripping the other welding techniques.
Due to the mentioned features, the laser welding now becomes an essential tool for manufacturing of medical items, electronics, batteries, parts with the necessity to have a precise, clean and narrow seam.
Flux-Cored Welding
Flux-cored welding is a very versatile welding process, and it is widely used in many industrial fabrication areas. It is like MIG welding except it uses a wire electrode that is filled with flux instead of a solid wire. The flux protects the weld pool by supplying a gas shield and slag to protect it from contamination in the atmosphere.
Flux-cored welding has a number of advantages for the industrial fabrication process, which implies. It gives a high deposition speed which means that welding is done faster and more efficiently. It can be also used for welding thick materials and it can be performed in any position. Flux-cored welding is another type of welding that is beneficial in outdoor and windy conditions because the flux offers better covering and protection against atmospheric elements.
Conclusion
Lastly, the MIG, TIG, Stick, Flux-Cored and laser welding techniques are the critical welding technologies that cater to the industrial manufacturing sector. The correct welding method is possibly to do with variables being joint design, material type of base, equipment cost requirements and performance expectations as well as other considerations. A description of standard industrial welding methods and their individual advantages can be beneficial for the fabricators to pick the most suitable one according to their specific needs of production.